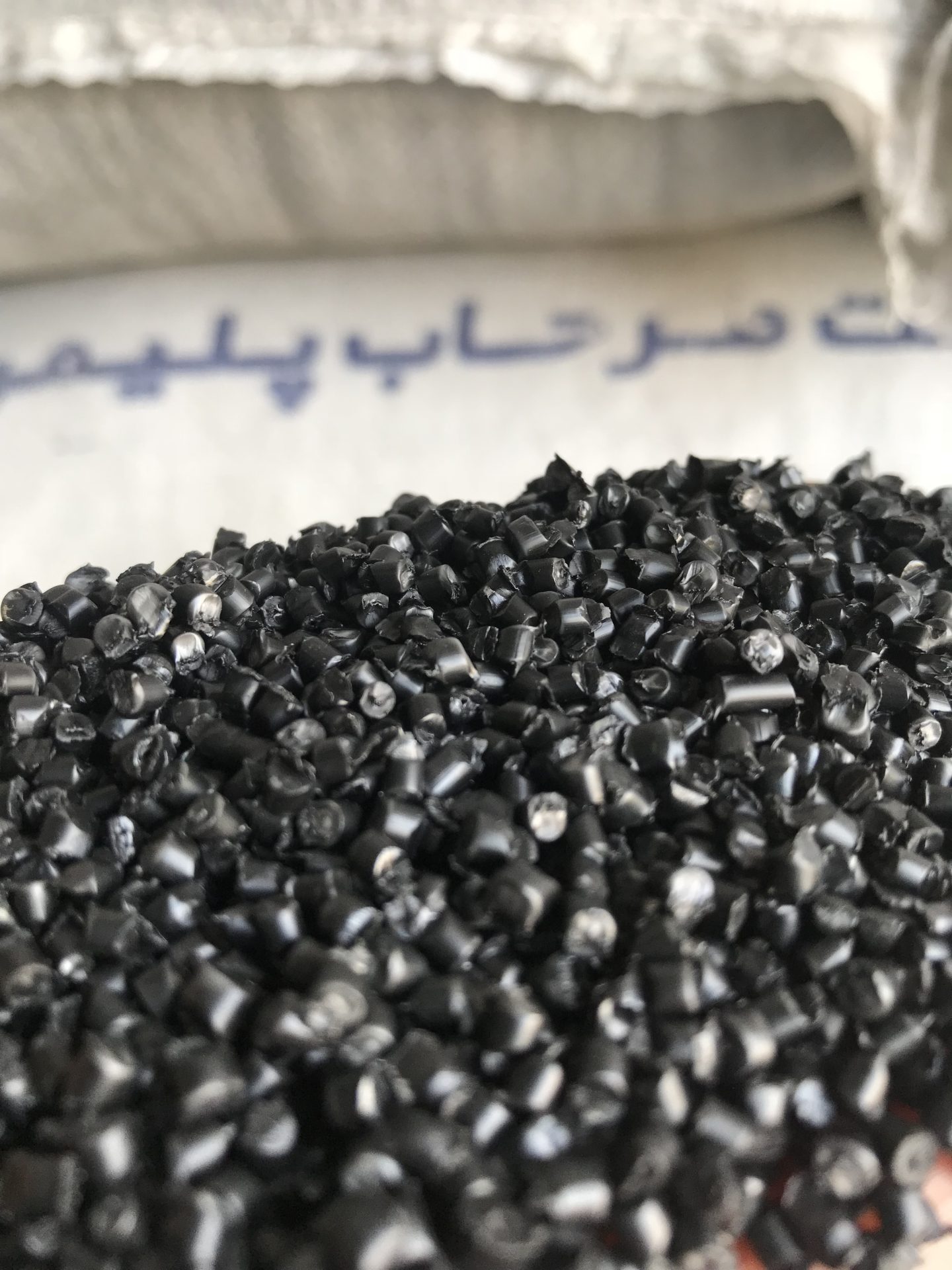
مقالات طرحاب پلیمر پیشرو
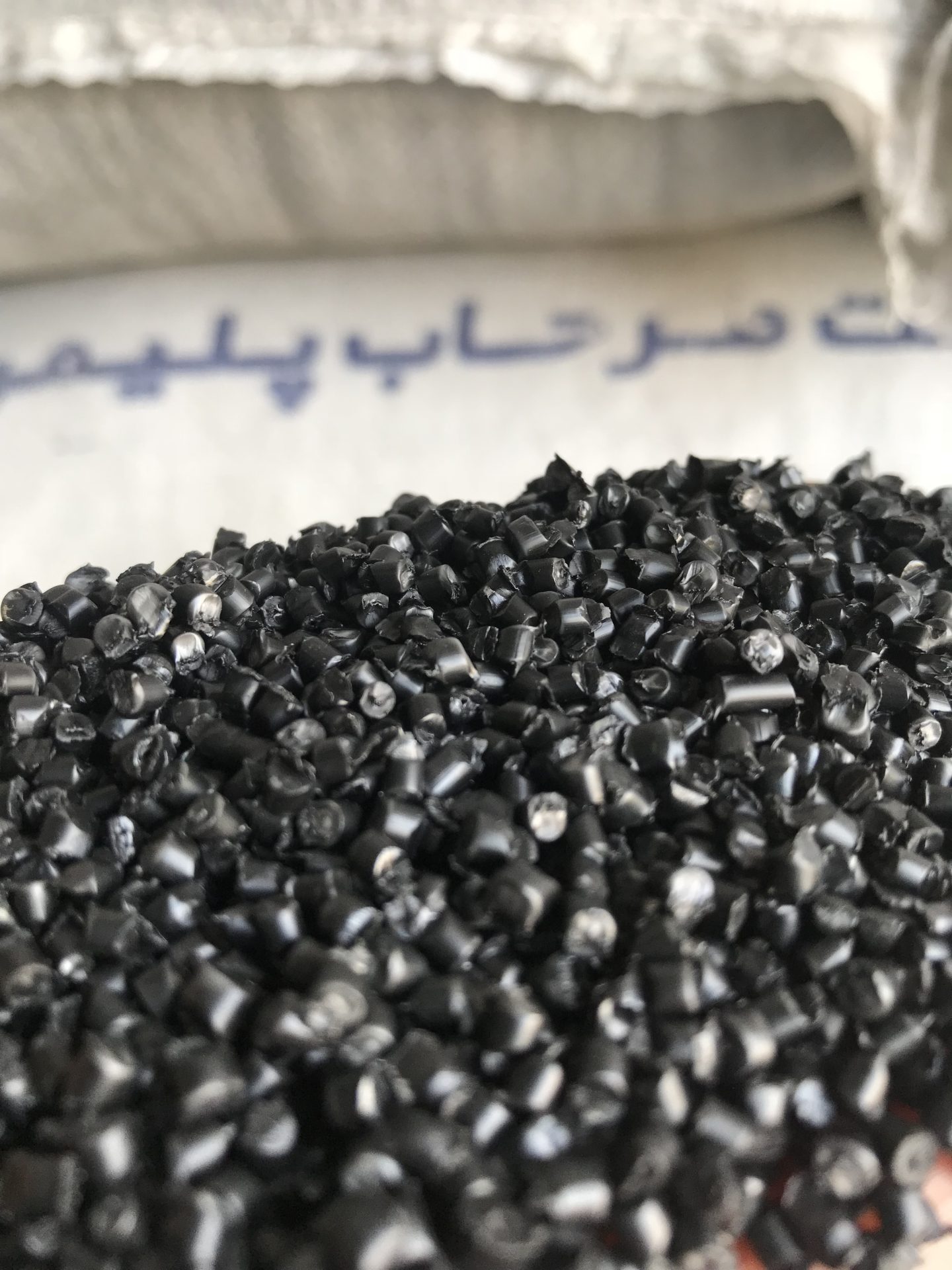
گرانول در صنایع بسیاری برای تولید محصولات پلاستیکی مورد استفاده قرار میگیرد و به دلیل سرعت بخشیدن به فرآیند تولیدات، مورد توجه تولید کنندگان زیادی قرار گرفته اند. در این بین، گرانول بازیافتی، به دلیل مزایای فراوانی که دارد، مورد توجه بسیاری از…

برای شناسایی پلیمرها روشهای مختلفی وجود دارد. یکی از آنها آزمون شعله است که ساده ترین روشی است که برای شناسایی پلیمرها میتوان انجام داد، از ویژگی های آزمون شعله سرعت انجام، سهولت و اقتصادی بودن این آزمایش است، ضمن این که مجموعه اطلاعات…
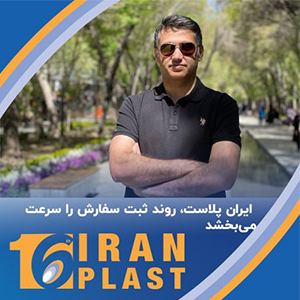
شرکت ایران پلاست امسال همانند سابق در نمایشگاه ایران پلاست ۱۴۰۱ شرکت میکند. غرفه این شرکت واقع در سالن میلاد B در ابتدای وروردی سالن میباشد . از همه شما عزیزان دعوت میشود در این رویداد مهم سالانه صنعت پلاستیک…
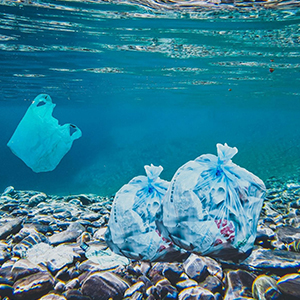
به گزارش پایگاه خبری بازیافت ایران به نقل از خبرنگار حوزه محیط زیست گروه اجتماعی باشگاه خبرنگاران جوان؛ زمین، خانه و آشیانه بشر و زیستمندان است، سیاره ای که انسان و موجودات زنده وابستگی متقابلی به آن دارند. بشر و زیستمندان برای…
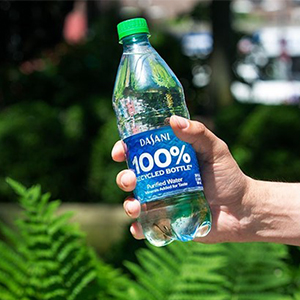
برندهای Dasani و Sprite شرکت Coca-Cola تغییراتی در بسته بندی پلاستیکی خود ایجاد کرده اند که برای حمایت از اقتصاد بازیافت طراحی شده است. داسانی بطری های ساخته شده از پلی اتیلن ترفتالات ۱۰۰ درصد بازیافتی (rPET) را بدون درپوش…
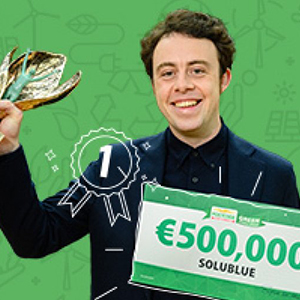
شرکت SoluBlue ، این استارت آپ بریتانیایی برای به دست آوردن این جایزه ۵۰۰ هزار یورویی با ۶۵۰ شرکت دیگر از سراسر قاره سبز رقابت شدیدی داشت و به عنوان پیروز این رقابت پایداری شناخته شد. حال این کمپانی می…
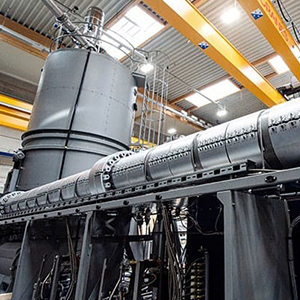
شرکت ارما اتریش سازنده ماشین آلات بازیافتی یکی از بزرگترین ماشین آلات بازیافت پت به گرانول پت را به ظرفیت ۴۰۰۰۰ تن در سال به مشتری خود در برزیل تحویل داد. مایکل هایتزینگر، مدیر عامل Erema می گوید: برای این…
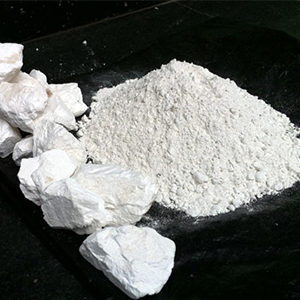
کربنات کلسیم یکی از مواد معدنی موجود در پوسته زمین است که با فرمول شیمیایی CaCO3 در طبیعت یافت میشود. علاوه بر آن، کربنات کلسیم را میتوان به طور مصنوعی و از ترکیب چند ماده در آزمایشگاه تولید کرد. دامنه…
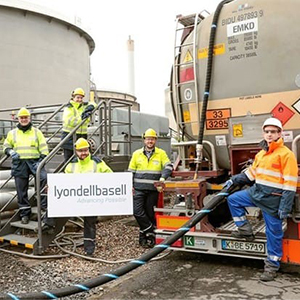
LyondellBasell شرکتی پلاستیکی ، مواد شیمیایی و تصفیه با دفتر مرکزی آمریکای شمالی در هوستون ، تولید پلیمرهای با کیفیت نو را از مواد اولیه به دست آمده از ضایعات پلاستیک در سایت Wesseling ، آلمان ، آغاز کرده است.…
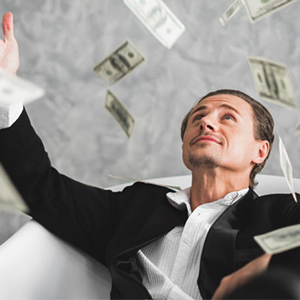
اگر یک جستجوی ساده در اینترنت داشته باشید، نکات، روشها و اصول زیادی برای موفقیتهای یکشبه وجود دارد و با کلیک روی این مطالب با حجم زیادی از پیشنهادها روبرو میشوید. حتی کلاسهای آموزشی، مقالهها، کتابها و ویدئوهای زیادی در…
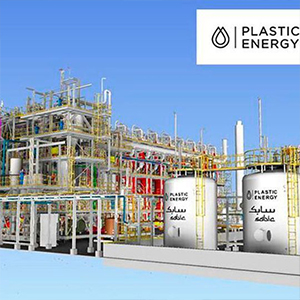
شرکت صنایع اساسی سعودی (SABIC) ، ریاض ، عربستان سعودی ، درحال ایجاد یک تفاهم نامه (MOU) با شرکت بازیافت سرمایه گذاری سعودی (SIRC) ، زیرمجموعه صندوق سرمایه گذاری عمومی عربستان (PIF) است،که اولین پروژه بازیافت مواد شیمیایی برای استفاده…
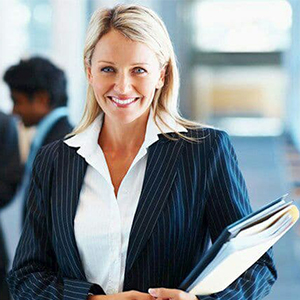
هبران موفق منتظر نمی مانند تا با اتفاقات جدید رو به رو شوند؛ بلکه خودشان این اتفاقات را برنامه ریزی کرده و شرایط را برای رخداد آنها مهیا می کنند. هر چقدر یک کسب و کار بیشتر رشد کند، میزان…
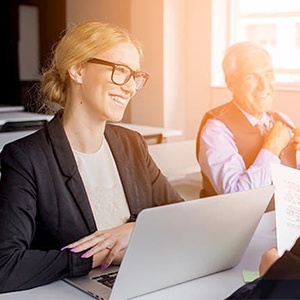
شاید به عنوان یک مدیر از عملکرد کارمندان خود ناراضی باشید؛ اما باید بدانید، هر جایگاهی احساس و درک متفاوتی دارد. کارآفرینان تا وقتی خود را جای کارمندان نگذارند، نمیتوانند به ایرادات و موانع موجود پی ببرند. اگر شما هم…
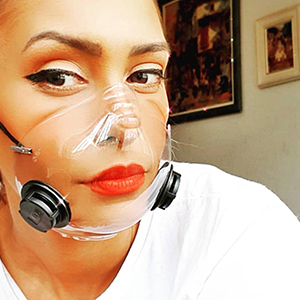
سپار/ایران پلیمرتولید ماسک های شفاف خصوصا برای ناشنوایان و اطرافیان آنها یک ضرورت برای برقراری ارتباط معمولی است. مطلع شدیم شرکت گرانول معصوم اخیرا آمیزه PVC خاصی را برای تولید این ماسک ها به بازار عرضه کرده است. خبرنگار ما…
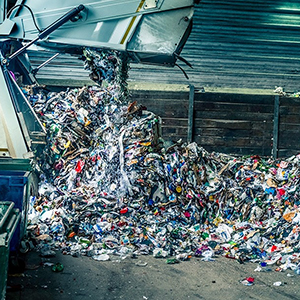
تحقیقات و نوآوری انگلستان (UKRI) ، سویندون ، انگلیس ، در حال سرمایه گذاری ۲۰ میلیون پوند (۲۵٫۸ میلیون دلار) در چهار کارخانه بازیافت است تا ظرفیت بازیافت موجود در انگلستان را افزایش دهد و دامنه پلاستیک های بازیافت شده…
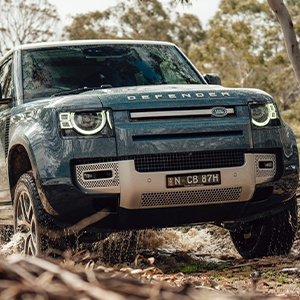
طبق گفته های این شرکت ، در مدل های بعدی جگوار و لندرور از کفپوش ساخته شده با الیاف نایلون اکونیل مشتق شده از مواد بازیافتی در تریم داخلی استفاده خواهد شد. جاگوار لندرور مستقر در انگلستان در تاریخ ۲۹…
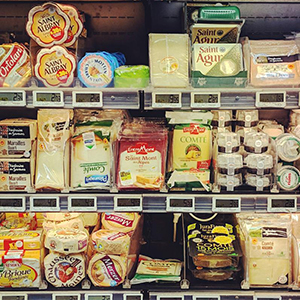
شرکت صنایع اساسی سعودی (SABIC) ، ریاض ، عربستان سعودی ، یک راه حل بسته بندی پایدار برای مواد غذایی منجمد راه اندازی کرده است که ترکیبی از یک درجه پلی اتیلن (PE) جدید با فناوری تولید فیلم است. وقتی…
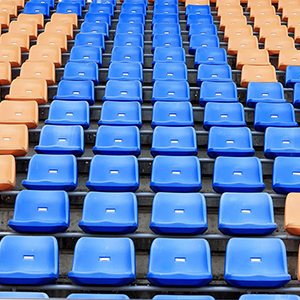
قطعات پلیمری مختلف در مدت زمان کاربری، دچار فرسودگی و پیرشدگی (Aging) می شوند. این فرایند به معنای کاهش خواص عمومی و مهندسی پلیمرها و نهایتا مناسب نبودن قطعه برای کاربری مورد نظر است. قرار گرفتن در محیط های مهاجم…
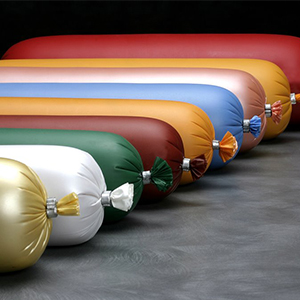
دو هدف اصلی استفاده از گریدهای مختلف پلی آمیدها در صنایع بسته بندی مواد غذایی، کاهش عبورپذیری در برابر اکسیژن، عطر، بو و افزایش خواص مکانیکی مانند مقاومت در برابر سوراخ شدگی است. دیگر خواص منحصر به فرد پلی آمید…
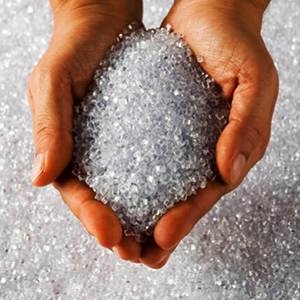
گریدهای مختلف گرانول بادی، استفاده های زیادی در بخش های مختلف صنعت دارند. از انواع گرانول بادی، میتوان به گریدهای BL3 و ۰۰۳۵ اشاره کرد. این نوع گرانولها به صورت شفاف، در دو نوع بی رنگ و چهار رنگ و به صورت رشته ای و خشک تولید میشوند. از انواع گریدهای گرانول…
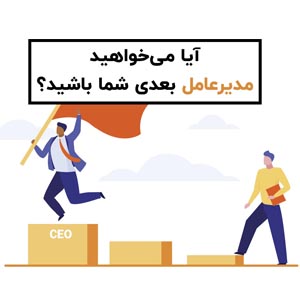
اگر قرار باشد که به زودی شما را به عنوان مدیرعامل جدید شرکتتان معرفی کنند، چه واکنشی نشان میدهید؟ عکسالعمل شما نسبت به این جایگاه شغلی ميتواند بسیاری از مسائل را روشن کند؛ مثلاً اینکه چگونه درباره شرکتتان فکر میکنید؟…
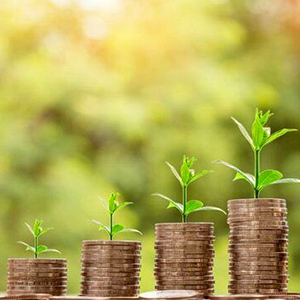
دنیایاقتصاد فهرست عناوین دنیایاقتصادجزئیات اولیهویژگیهای اوراقپیام اقتصاد سیاسی وعده «گشایش اقتصادی» رمزگشایی شد. دولت قرار است اوراق سلف موازی با پشتوانه نفت خام را عرضه کند. شنیدههای اولیه حاکی از آن است که در این طرح ۲۲۰ میلیون بشکه در…
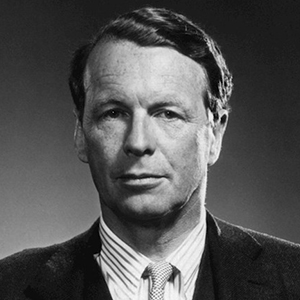
بازاریابی حرفهای نیست که هر کس در آن موفق شود، زیرا نظریههای بازاریابی هر ۱۰ سال یک بار تغییر می کند. البته “دیوید آگیلوی” نظریات ارزشمند و پایداری دارد که به اندازه یک قرن می توان روی آنها تکیه کرد. با یوکن همراه…
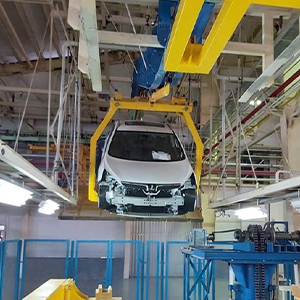
با وجودی که صنعت خودرو ایران یکی از نخستین اهداف تحریم های ناجوانمردانه آمریکا بود اما نشان داد که نه تنها این فشارها موجب توقف این صنعت نمی شود بلکه با تلاش فعالان این حوزه پیشرفت های چشمگیری نیز حاصل…
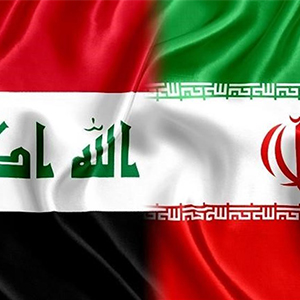
به گزارش خبرگزاری مهر به نقل از بانک مرکزی، حمید قنبری، مدیرکل بینالملل بانک مرکزی که روز یکشنبه هفته جاری به همراه وزیر امور خارجه برای انجام مذاکرات بانکی به عراق سفر کرده بود، گفت: در این دیدار مذاکرات مفید و سازندهای با طرف…
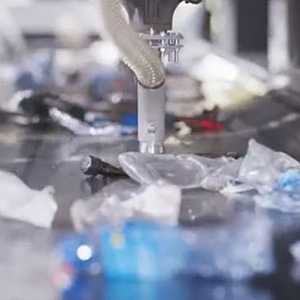
شرکت بازیافت Tomra Sorting ، در آلمان ، بخشی از گروه Tomra نروژ ، در ژوئن از یک رویداد آنلاین استفاده کرد تا فناوری های مرتب سازی جدید برای چندین برنامه مختلف بازیافت را اعلام کند. نمایشگاه آنلاین “سمفونی همه…
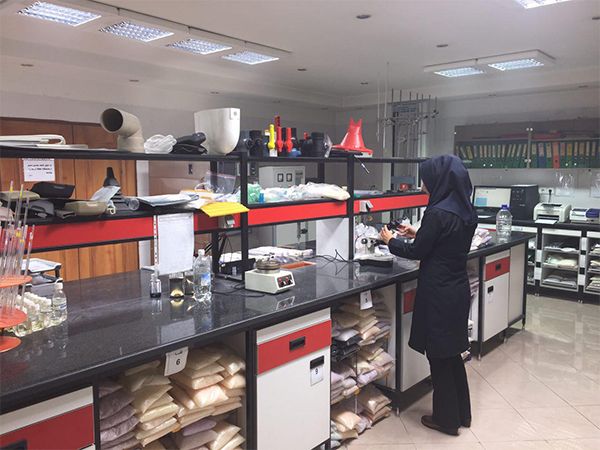
الاستومر گرمانرم یا TPE و یا TPR،مخفف لاستیک های گرمانرم است.نوع الاستومر با پلاستیک تشکیل شده تحت درجه حرارت نرمال است. ویژگی ساختار ترموپلاستیک (الاستومرهای مختلف) پیوند شیمیایی رزین و لاستیک با فرم زنجیره ی اتصال فیزیکی بین نیروهای اتمی…
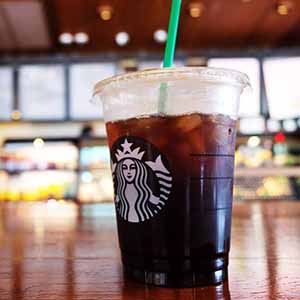
طبق گزارش جدیدی که برای ردیابی پیشرفت شرکت ها در افزایش استفاده از پلاستیک بازیافت شده استفاده می شود ، رزین بازیافتی درصد کمی از کل پلاستیک های مورد استفاده در Cocacola ، Starbucks و دیگران را تشکیل می دهد.…
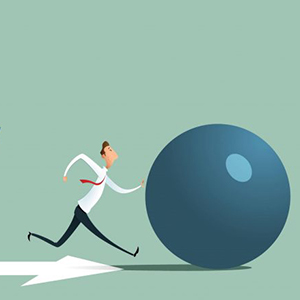
اگر گاهی اوقات در مورد اینکه در طول یک روز کاری خود چقدر عملکرد کمی داشتهاید، ناامید شدهاید؛ شما تنها نیستید. تحقیقات نشان میدهد که تنها ۲۶ درصد از افراد، غالبا بعد از انجام دادن وظایف موردنظرشان، با رضایت کامل…
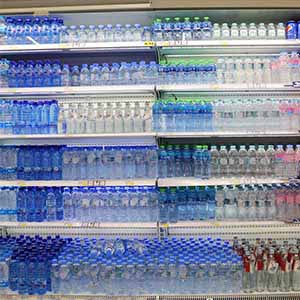
چهار نوآوری در لیبل ها که از مشکلات در فرآیند بازیافت PET جلوگیری می کند ، اخیراً در انجمن بازیافت پلاستیک (APR) معرفی شده است. در ماه مارس این انجمن نامه هایی صادر كرد كه تأیید می كرد كه دو…
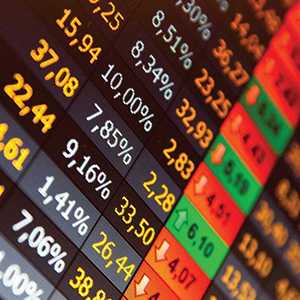
احمد خادم المله، مدیرمسئول اقتصاد برتر: این روزها با هر کس صحبت میکنی یا بدنبال گرفتن کد در بورس است و یا پای کامپیوتر بورس بازی و خرید و فروش سهام می کند. برای من خیلی جای تعجب بود که…
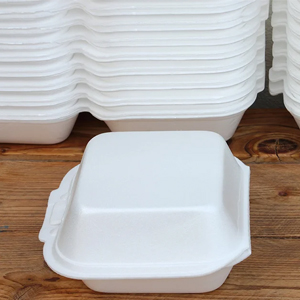
لایحه ای که در ۱۷ فوریه توسط مجلس سنا در واشنگتن به تصویب رسید ، به منظور کاهش آلودگی با ممنوعیت فروش و توزیع محصولات پلی استایرن منبسط شده (Styrofoam) طراحی شده است. به گزارش روزنامه آبرن خبرنگار ، این…
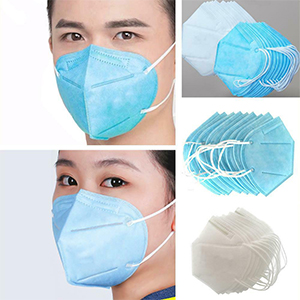
قیمت انواع تجهیزات پزشکی یکبار مصرف به دلیل کاهش محموله آنها از چین به عنوان تأثیر شیوع کرونا ویروس کشنده ، طی دو هفته گذشته روند صعودی را نشان داده است. این مقاله کشور بنگلادش را در حوادث اخیر بررسی…
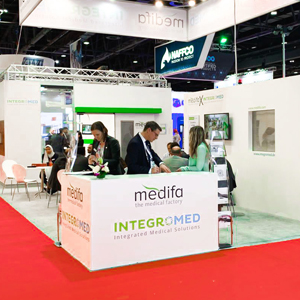
انتشار ویروس کرونا نشان داد که بهداشت جهانی چقدر آسیبپذیر است. تقویت ارتباط سازمانهای بهداشتی کلید مهار چنین بیماریهایی است و این دقیقا موضوع نمایشگاه بهداشت عربی ۲۰۲۰ است. سازمانهای پزشکی میتوانند در زمان بحران با هوش مصنوعی اطلاعات را…
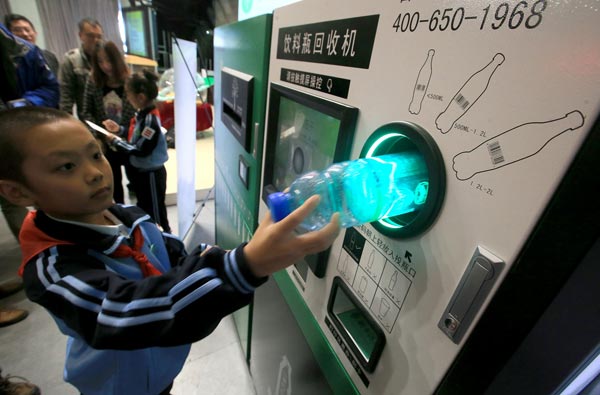
برای بلیط مترو رم پول کافی ندارید؟ جای نگرانی نیست ، فقط چند بطری پلاستیکی را جمع کنید و به راحتی می توانید سوار شوید. پایتخت ایتالیا به مسافران راهی برای تبادل بطری های پلاستیکی زباله خود برای بلیط…
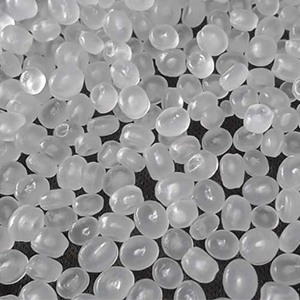
برای پیش بینی رشد تقاضای پلی اتیلن باید عوامل زیادی از جمله تقاضای مصرف کننده، درامد و رشد صنعت پکیجینگ، که بزرگترین مصرف کننده پلی اتیلن است را در نظر گرفت. تمام متغیرهای بالا به رشد تولید ناخالصی داخلی ارتباط…
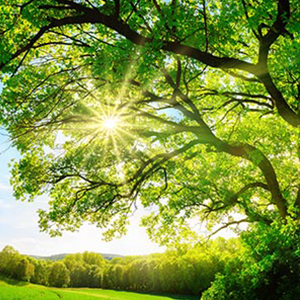
سازمان امور مالیاتی کشور، عوارض جدید تولید یا واردات کالاهای دارای پسماند «مخرب محیط زیست» را اعلام کرد. در راستای اجرای صحیح مقررات تولیدکنندگان و واردکنندگان مکلفند ضمن ارائه اظهار نامه این بند در پایان هر دوره مالیاتی موضوع قانون…
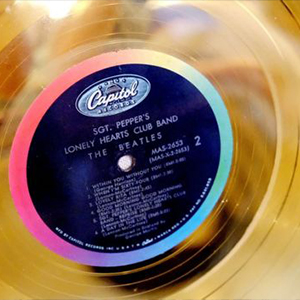
آیا پلاستیک هنوز جذاب است؟ امروز ما دریافتیم که پلاستیک یک تهدید بزرگ برای محیط زیست است اما برای دلایل محکمی وجود داشته که ما انسانها عاشق این ماده ساخت بشر شدهایم. پروفسور مارک میودووینک، محقق مواد و استاد دانشگاه…
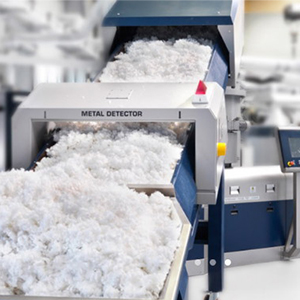
به گزارش طرحاب پلیمر به نقل ازmrcplast.com ، شرکتهای بوریالیس، تولیدکننده پلیالفین و ارما (Erema)، تولیدکننده ماشینآلات بازیافت، بهعنوان دو بازیگر کلیدی صنعت پلاستیک اتریش، به تازگی توافقنامهای (LOI) را برای تقویت همکاریها در زمینه توسعه ماشینآلات بازیافت امضا کردند. این…
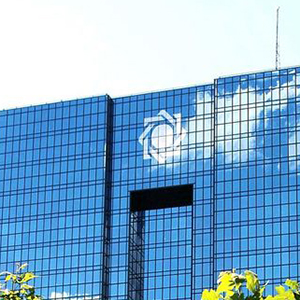
بانک مرکزی، جزییات بسته سیاستی نحوه برگشت ارز حاصل از صادرات در سال ۱۳۹۸ را اعلام کرد و بر اساس آن ۶۰ درصد ارز صادرات پتروشیمی و ۵۰ درصد ارز سایر محصولات صادراتی به کشور برگشته است.به گزارش آرمان اقتصادیو به…
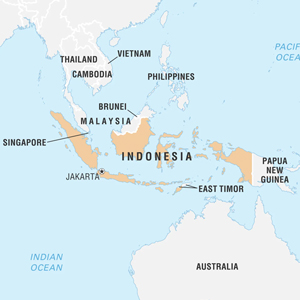
شرکت بریتانیایی پلاستیک انرژی در نظر دارد پنج مجتمع بازیافت پلاستیک را در غرب جاوه کشور اندونزی احداث کند. به گزارش نیپنا به نقل از پلاستیک نیوز یوروپ (plasticsnewseurope)، شرکت بریتانیایی پلاستیک انرژی (Plastic Energy) سوم آوریل اعلام کرد که…
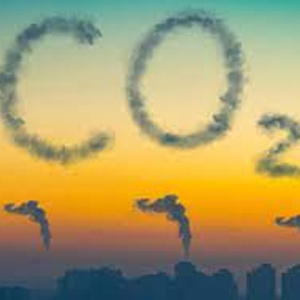
ممکن است یک منبع پنهانی از گازهای گلخانه ای وجود داشته باشد که ما به آن توجه نمی کنیم. تحقیقات جدیدی از دانشگاه هاوایی در Manoa نشان می دهد که پلاستیک در اثر تابش نور ممکن است گازهایی منتشر کند…
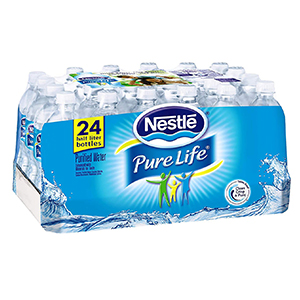
موسسه صنایع بازیافت ضایعات (ISRI)، واشنگتن،جایزه خود را به ، استامفورد، Nestlé Waters North America (NWNA) DFR) بخاطر استفاده نوآورانه از پلاستیک بازیافت شده و طراحی محصولش با تمرکز بر بازیافت، به عنوان طراحی ۲۰۱۹ برای بازیافت اهدا کرد. جایزه DFR…
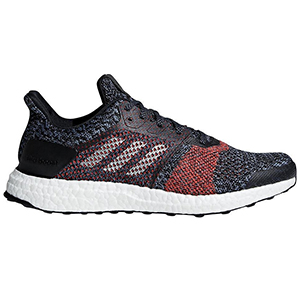
در سال ۲۰۱۸، Adidas بیش از پنج میلیون جفت کفش حاوی ضایعات پلاستیکی بازیافتی را تولید کرد. این شرکت در حال حاضر قصد دارد این رقم را بیش از دو برابر کند. به عنوان نتیجه همکاری بین سازنده محصولات ورزشی…
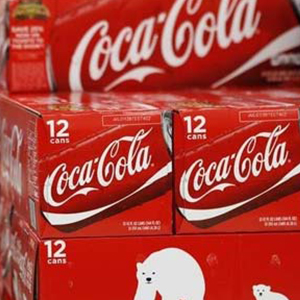
برای نخستین بار، کوکاکولا فاش کرده که برای تهیه محصولات خود در یک سال از سه میلیون تن پلاستیک استفاده کرده است. گزارش بنیاد الن مکآرتور در این زمینه، به شرکتها و دولتها فشار میآورد تا برای مقابله با آلودگی…
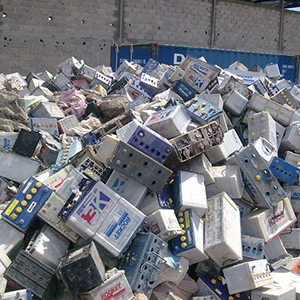
این مقاله، بازار وسيع ماشين هايي با باتري هاي پيشرفته تا زماني كه باتري ها بازيافت شوند را برسي ميكند . این سیستم ، بازیافت را با استفاده از بازیافت باتری اسید سرب به عنوان یک مدل توصيف ميكند .…
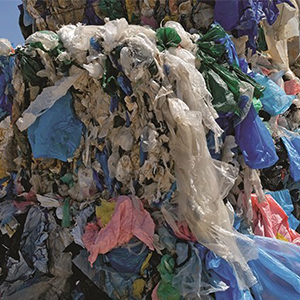
طبق دو گزارش شورای شیمی آمریکا (واشنگتن)، بازیافت پلاستیک های غیر بطری سفت و سخت، کیسه ها و بسته بندی انعطاف پذیر فیلم (که در مجموع به عنوان فیلم شناخته می شود) در سال ۲۰۱۶ به میزان ۱۰ درصد افزایش…
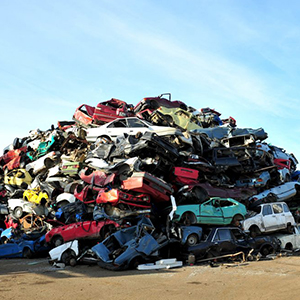
تصور کنید اگر اتومبیل ها ۱۰۰ درصد قابل بازیافت باشند. در پایان عمر مفید آنها می توان به راحتی از هم جدا شده و اکثر قطعات به عنوان جایگزینی فروخته می شوند یا به عنوان مواد اولیه برای قطعات جدید…
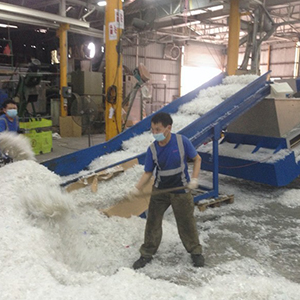
طبق برآوردهای یک سازمان بازیافت پلاستیک چینی، پلاستيك هاي بازيافتي ( مصرف شده ) وارد شده به چین در سال جاری احتمالا از سال ۲۰۱۷ به میزان قابل توجهی کاهش می یابد، احتمالا ۵ درصدِ مقدار سال گذشته است. استیو…